【秦先生11期陌陌艺校小琴】最新入口
-
Types and price ranges of mixed gas compressors
Jun 09, 2024 -
piston gas compressor types, and price examples
May 13, 2024 -
Requirements for Nitrogen Compressors in Industrial Nitrogen Compression
Jul 18, 2024 -
20 hydrogen compressor manufacturers in china and price range of compressor
Jun 24, 2024 -
Requirements for wellhead gas compression for wellhead gas compressors
Jul 16, 2024 -
Functions and working principles of a natural gas compressor
Jul 13, 2024
秦先生11期陌陌艺校小琴【乾坤易变】Apr 11, 2024
by:Anhui Shengnuo Compressor Manufacturing Co.,Ltd
Follow Us:
Casing gas refers to the natural gas produced along with oil in an oil well. When oil is extracted from the reservoir, casing gas is also brought to the surface. Casing gas can be a byproduct of oil production and is often considered a waste or associated gas. A casing gas compressor, also known as a casing gas injection compressor, is a type of compressor used in the oil and gas industry. It is specifically designed to handle the compression of casing gas.
Casing gas injection compressors are used to compress the casing gas and inject it back into the reservoir or use it for other purposes. The compressor increases the pressure of the casing gas to the desired level for reinjection or for utilization in other processes, such as power generation or fuel gas supply.
These compressors are typically designed to handle the specific characteristics of casing gas, including its composition, pressure, and flow rate. They are typically robust and reliable to withstand the demanding conditions of the oil and gas industry.
Casing gas injection is an important practice in oil and gas production as it helps maintain reservoir pressure, maximize oil recovery, and prevent environmental emissions. Casing gas compressors play a vital role in this process by providing the necessary compression capabilities.
【秦先生11期陌陌艺校小琴】注册登录
Casing gas compressors have various applications in the oil and gas industry. Here are some common applications:
1. Casing Gas Re-Injection: One of the primary applications of casing gas compressors is to compress the produced casing gas and inject it back into the reservoir. This re-injection helps maintain reservoir pressure, enhance oil recovery, and prevent the flaring or venting of associated gas, reducing greenhouse gas emissions.
2. Gas Lift Systems: Casing gas compressors can be used in gas lift systems, which are employed to lift oil from the wellbore to the surface. The compressed casing gas is injected into the wellbore through gas lift valves, creating artificial lift and facilitating oil production.
3. Fuel Gas Supply: Casing gas compressors can compress the casing gas to the required pressure for utilization as fuel gas. The compressed casing gas can be used in heaters, boilers, furnaces, or power generation units on-site, reducing the need for external fuel sources.
4. Gas Gathering and Processing: Casing gas compressors are utilized in gas gathering and processing facilities to compress the casing gas for transportation through pipelines. The compressed gas can be further processed, treated, or separated into different components for commercial use or sale.
5. Vapor Recovery Units (VRUs): Casing gas compressors are employed in vapor recovery units to compress and recover volatile organic compounds (VOCs) and hydrocarbon vapors emitted during oil and gas production processes. The recovered vapors can be processed, treated, or recycled, reducing emissions and improving environmental sustainability.
6. Flare Gas Recovery: Casing gas compressors can also be used in flare gas recovery systems to capture and compress the casing gas that would otherwise be flared or vented into the atmosphere. The compressed gas can then be utilized for various purposes, such as fuel, re-injection, or commercial sale.
These are just a few examples of the applications of casing gas compressors. The specific application depends on the operational requirements, gas composition, and goals of the oil and gas production facility. Casing gas compressors play a crucial role in maximizing resource utilization, reducing emissions, and enhancing operational efficiency in the oil and gas industry.
【秦先生11期陌陌艺校小琴】平台地址
There are different types of casing gas compressors used in the oil and gas industry, each with its own design and operating characteristics. Here are some common types:
1. Reciprocating Compressors: Reciprocating compressors, also known as piston compressors, use a piston-cylinder arrangement to compress the casing gas. They are known for their high efficiency, wide operating range, and ability to handle varying gas compositions. Reciprocating compressors can be either single-acting or double-acting, depending on the number of compression stages.
2. Rotary Screw Compressors: Rotary screw compressors use two interlocking helical rotors to compress the casing gas. They are known for their continuous and smooth operation, high capacity, and compact design. Rotary screw compressors are often used for higher flow rates and can handle a wide range of gas compositions.
3. Centrifugal Compressors: Centrifugal compressors use centrifugal force to compress the casing gas. They consist of an impeller that rotates at high speeds, accelerating the gas and converting kinetic energy into pressure energy. Centrifugal compressors are suitable for high-capacity applications and can handle large flow rates at relatively lower compression ratios.
4. Axial Compressors: Axial compressors use a series of rotating blades to compress the casing gas. They are commonly used in large-scale gas processing and transmission systems. Axial compressors are known for their high efficiency and are capable of handling high flow rates.
5. Screw-Scroll Compressors: Screw-scroll compressors combine the principles of rotary screw and scroll compressors. They use a pair of intermeshing spiral rotors and a stationary scroll to compress the casing gas. Screw-scroll compressors offer improved efficiency, compactness, and quiet operation.
6. Liquid Ring Compressors: Liquid ring compressors use a liquid ring created by centrifugal force to compress the casing gas. They are suitable for handling wet or contaminated gases and can tolerate liquid carryover. Liquid ring compressors are often used in applications where corrosion resistance is crucial.
7. Diaphragm Compressors: Diaphragm compressors use a flexible diaphragm to compress the casing gas. They provide a seal between the compression chamber and the driving mechanism, making them suitable for handling toxic, corrosive, or explosive gases. Diaphragm compressors are commonly used in applications with stringent safety and environmental requirements.
8. Jet Compressors: Jet compressors, also known as ejectors, use a high-pressure motive gas or steam to entrain and compress the casing gas. They are simple in design, require no moving parts, and are often used for low-pressure applications. Jet compressors are energy-efficient and can handle a wide range of gas compositions.
9. Scroll Compressors: Scroll compressors use two interleaving spiral scrolls to compress the casing gas. They are known for their compact size, quiet operation, and high efficiency. Scroll compressors are commonly used in smaller-scale applications where space and noise considerations are important.
10. Lobe Compressors: Lobe compressors, also called Roots blowers, use a pair of rotating lobes to compress the casing gas. They provide pulsation-free flow and are suitable for applications requiring high flow rates at relatively low compression ratios. Lobe compressors are often used in pneumatic conveying systems and wastewater treatment plants.
The selection of the casing gas compressor type depends on various factors such as gas composition, flow rate, pressure requirements, efficiency considerations, and available space. Each compressor type has its own advantages and limitations, and the choice depends on the specific application and operational requirements of the oil and gas facility.
【秦先生11期陌陌艺校小琴】娱乐全站
The price range of casing gas compressors can vary significantly depending on several factors, including the compressor type, capacity, brand, specifications, and market conditions. Additionally, pricing information can fluctuate over time. However, to provide a general idea, here are some approximate price ranges for casing gas compressors:
1. Reciprocating Compressors: The price range for reciprocating casing gas compressors can vary from $10,000 to $100,000 or more, depending on the capacity and specifications of the compressor.
2. Rotary Screw Compressors: The price range for rotary screw casing gas compressors typically starts from around $20,000 and can go up to several hundred thousand dollars, depending on the capacity and features.
3. Centrifugal Compressors: Centrifugal casing gas compressors are usually more expensive compared to other types. The price range for centrifugal compressors can start from several hundred thousand dollars and go up to several million dollars, depending on the capacity and configuration.
4. Other Compressor Types: The price range for other types of casing gas compressors, such as axial compressors, liquid ring compressors, diaphragm compressors, and jet compressors, can vary widely depending on their capacity and specifications. Prices can range from several thousand dollars to several hundred thousand dollars, depending on the specific requirements.
It's important to note that these price ranges are approximate and can vary significantly based on the factors mentioned above. To get accurate and up-to-date pricing information for casing gas compressors, it is recommended to contact authorized equipment dealers, manufacturers, or suppliers who can provide detailed quotes based on your specific needs and specifications.
【秦先生11期陌陌艺校小琴】体育直播

Hi! Welcome back.
How are you doing?
Let s talk! We’ll provide the perfect solution for you!
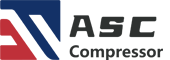
Since its establishment, ASC Compressor has focused on comprehensive solutions for Oilfield industry, CNG/LNG industry, Environmental protection, and Industrial compression. It has excellent quality in designing, researching, producing and manufacturing.
- Quick Link > Home > Products > Applications > News > About > Contact
-
Contact Us
- E-Mail: [email protected]
- Tel: +8618098536798/+86(0)5633698699
- Fax: +86(0)5633698699
-
Address:
No. 17 Xingye Road, Economic Development Zone, Xuanzhou District, Xuancheng City, Anhui Province, China