【三年成都中文在线观看免费版】最新入口
-
Price range of compressors for different gases
Jul 17, 2024 -
Requirements for ammonia compressors in different application industries
Jul 24, 2024 -
Functions and working principles of a natural gas compressor
Jul 13, 2024 -
Functions of casing gas compressor
Apr 25, 2024 -
Features and price range of reciprocating piston chlorine compressors
May 21, 2024 -
How to choose a natural gas compressor
Jul 06, 2024
三年成都中文在线观看免费版【乾坤易变】Jul 03, 2024
by:Anhui Shengnuo Compressor Manufacturing Co.,Ltd
Follow Us:
Corrosion in a chlorine gas compressor can be a significant concern due to the highly corrosive nature of chlorine gas. Here are some measures to help avoid corrosion in chlorine gas compressors:
1. Material Selection: Choose materials that are resistant to chlorine gas and its corrosive effects. Stainless steel alloys, such as 316L or Hastelloy, are commonly used for components that come into contact with chlorine gas. Consult with compressor manufacturers or corrosion specialists to determine the most suitable materials for your specific application.
2. Protective Coatings: Apply appropriate protective coatings on compressor surfaces that may come into contact with chlorine gas. These coatings can provide an additional barrier against corrosion. Consult with coating specialists to select coatings that are compatible with chlorine gas and can withstand the operating conditions of the compressor.
3. Proper Ventilation: Ensure that the compressor room or area is well-ventilated to prevent the accumulation of chlorine gas. Adequate ventilation helps to reduce the concentration of corrosive gases in the air, minimizing the potential for corrosion on compressor surfaces.
4. Moisture Control: Moisture in the compressor system can accelerate corrosion. Implement measures to control moisture, such as proper drainage, condensate removal, and the use of moisture separators or dryers in the gas supply line. Keeping moisture levels low can help mitigate corrosion risks.
5. Regular Inspection and Maintenance: Conduct regular inspections of the compressor system to identify any signs of corrosion or damage. Pay particular attention to areas exposed to chlorine gas. Implement a maintenance program that includes cleaning, lubrication, and replacement of worn or damaged parts to prevent corrosion from progressing.
6. Corrosion Monitoring: Consider implementing a corrosion monitoring program to track the corrosion rates and conditions within the compressor system. This can help identify any potential corrosion issues early on and allow for timely corrective actions.
7. Proper Chlorine Gas Handling: Follow proper procedures for handling and storing chlorine gas to minimize leaks and spills. Ensure that safety measures are in place to prevent exposure to chlorine gas, as well as to contain any potential leaks or releases.
8. Regular Cleaning: Keep the compressor and its components clean to prevent the accumulation of corrosive substances, such as dust, dirt, or chlorine residues. Use suitable cleaning methods and materials that are compatible with the compressor's construction and the corrosive nature of chlorine gas.
9. Gas Purification: Implement a gas purification system to remove impurities, contaminants, and moisture from the chlorine gas stream before it enters the compressor. Purifying the gas can help reduce the potential for corrosion caused by impurities or moisture.
10. Proper System Design: Ensure that the compressor system is designed with corrosion prevention in mind. Consider factors such as proper drainage, avoidance of dead zones where corrosive gases can accumulate, and appropriate sealing to prevent gas leaks. Engaging experienced engineers or consultants familiar with chlorine gas systems can help optimize the design for corrosion resistance.
11. Corrosion Inhibitors: Consider using corrosion inhibitors specifically formulated for chlorine gas applications. These inhibitors can be added to the gas stream or applied to the compressor surfaces to provide an additional layer of protection against corrosion.
12. Education and Training: Provide proper education and training to personnel involved in operating and maintaining chlorine gas compressors. Ensure they are aware of the corrosive nature of chlorine gas, understand the necessary precautions, and are trained in proper handling, maintenance, and safety procedures.
13. Regular System Monitoring: Implement a comprehensive monitoring program to assess the condition of the compressor system and detect any signs of corrosion. This can include regular inspections, corrosion rate measurements, and analysis of corrosion monitoring data. Prompt action can be taken if any corrosion-related issues are identified.
14. Compliance with Standards: Adhere to applicable industry standards, guidelines, and regulations related to chlorine gas handling, compressor design, and corrosion prevention. These standards provide valuable recommendations and requirements for safe and corrosion-resistant operation.
Remember, corrosion prevention in chlorine gas compressors is a critical aspect to ensure safe and reliable operation. Consultation with experts in the field, adherence to best practices, and regular maintenance are key to avoiding corrosion and maximizing the lifespan of the compressor system.
If you encounter corrosion in a chlorine compressor, it's important to take prompt action to address the issue. Here are some steps to consider if your chlorine compressor is corroded:
1. Safety First: Prioritize safety by following proper procedures for handling chlorine gas and ensuring the appropriate personal protective equipment (PPE) is used. If there is a risk of gas leakage or exposure, evacuate the area and contact emergency authorities if necessary.
2. Assess the Extent of Corrosion: Evaluate the severity and extent of the corrosion in the compressor. Inspect all affected components, including valves, cylinders, piston rings, and any other areas exposed to chlorine gas. Determine if the corrosion is localized or widespread.
3. Halt Operation: If the corrosion is severe or poses a risk to the safe operation of the compressor, shut down the compressor immediately. Continuing to operate a corroded compressor can lead to further damage, reduced efficiency, and potentially dangerous conditions.
4. Consult a Specialist: Seek guidance from compressor manufacturers, corrosion specialists, or professionals experienced in chlorine gas systems. They can provide expert advice on the best course of action based on the specific corrosion situation and the compressor's design.
5. Repair or Replace Corroded Parts: Depending on the extent of corrosion and the condition of the affected components, you may need to repair or replace them. Corroded parts may require cleaning, sandblasting, or abrasive cleaning to remove the corrosion and restore the surface. In more severe cases, parts may need complete replacement to ensure safe and reliable operation.
6. Consider Material Upgrades: Evaluate if there is a need to upgrade the materials used in the compressor to better withstand chlorine gas corrosion. Consult with experts to determine if different materials or coatings should be employed to enhance corrosion resistance.
7. Implement Preventive Measures: Once the corrosion issue has been addressed, take preventive measures to avoid future corrosion. This may include implementing the preventive measures discussed earlier, such as material selection, coatings, proper ventilation, moisture control, and regular maintenance.
8. Monitor and Maintain: Establish a monitoring and maintenance program to regularly inspect the compressor for signs of corrosion and address any potential issues promptly. This includes routine cleaning, lubrication, and adherence to recommended maintenance schedules.
9. Perform System Flush: If the corrosion has resulted in the accumulation of corrosive residues or contaminants in the compressor system, it may be necessary to perform a thorough system flush. This involves cleaning out the entire system, including pipes, valves, and other components, to remove any remaining corrosion products and contaminants. Consult with experts to determine the appropriate cleaning method and cleaning agents compatible with chlorine gas systems.
10. Analyze the Root Cause: Investigate and identify the root cause of the corrosion in the chlorine compressor. Corrosion can result from various factors, such as inadequate material selection, poor system design, improper maintenance, or exposure to impurities. Understanding the underlying cause will help prevent similar corrosion issues in the future.
11. Implement Corrosion Prevention Measures: Based on the analysis of the root cause, implement appropriate corrosion prevention measures to mitigate the risk of future corrosion. This may include upgrading materials, modifying system design, implementing additional protective coatings, enhancing ventilation and moisture control, or adjusting maintenance practices.
12. Document and Learn from the Experience: Keep detailed records of the corrosion incident, the actions taken, and the outcomes. This information will be valuable for future reference and can help in improving corrosion prevention strategies and maintenance practices. Share the knowledge gained from the experience with relevant personnel to enhance awareness and prevent similar issues in other chlorine gas systems.
13. Regularly Monitor and Inspect: Following the resolution of the corrosion issue, establish a regular monitoring and inspection routine for the chlorine compressor. This includes monitoring corrosion rates, conducting visual inspections, and performing scheduled maintenance tasks. Early detection of any corrosion signs will allow for timely intervention and minimize the risk of major corrosion-related problems.
14. Training and Education: Provide training and education to personnel involved in operating and maintaining the chlorine compressor system. Ensure they are knowledgeable about corrosion prevention measures, safety protocols, and proper handling of chlorine gas. Regularly update their training to keep them informed about the latest practices and technologies related to corrosion mitigation.
By following these steps and implementing appropriate measures, you can effectively address corrosion in a chlorine compressor and work towards preventing future corrosion-related issues. Remember to consult with experts in the field and adhere to industry best practices to ensure safe and reliable operation of the compressor system.
【三年成都中文在线观看免费版】注册登录

Hi! Welcome back.
How are you doing?
Let s talk! We’ll provide the perfect solution for you!
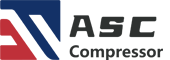
Since its establishment, ASC Compressor has focused on comprehensive solutions for Oilfield industry, CNG/LNG industry, Environmental protection, and Industrial compression. It has excellent quality in designing, researching, producing and manufacturing.
- Quick Link > Home > Products > Applications > News > About > Contact
-
Contact Us
- E-Mail: [email protected]
- Tel: +8618098536798/+86(0)5633698699
- Fax: +86(0)5633698699
-
Address:
No. 17 Xingye Road, Economic Development Zone, Xuanzhou District, Xuancheng City, Anhui Province, China