【男生把困困放到女生困困视频高清】最新入口
-
Requirements for ammonia compression for ammonia compressors
Jul 29, 2024 -
Some prominent butadiene compressor manufacturers in China
Jun 27, 2024 -
Features And Applications Of CNG Standard Station Compressor
May 30, 2024 -
The Applications, Types, And Price Ranges Of Casing Gas Compressors
Apr 11, 2024 -
Compressors used for natural gas recovery, and price ranges
Jun 17, 2024 -
Requirements for ammonia compressors in different application industries
Jul 24, 2024
男生把困困放到女生困困视频高清【乾坤易变】May 24, 2024
by:Anhui Shengnuo Compressor Manufacturing Co.,Ltd
Follow Us:
The working principle of a chlorine compressor is based on the principles of positive displacement compression. Chlorine compressors are typically reciprocating compressors, which means they use a piston and cylinder arrangement to compress the gas.
Here is an overview of the working principle of a chlorine compressor:
1. Suction Stroke: The compressor begins the cycle with the suction stroke. The piston moves downward, creating a low-pressure zone within the cylinder. This low-pressure zone allows the chlorine gas to enter the cylinder through the suction valve. The suction valve opens during this stroke, allowing the gas to flow into the cylinder.
2. Compression Stroke: Once the suction stroke is completed, the piston reverses its direction and moves upward, starting the compression stroke. As the piston moves upward, it compresses the chlorine gas within the cylinder. The compression stroke causes the pressure of the gas to increase.

3. Discharge Stroke: At the end of the compression stroke, the discharge valve opens, allowing the compressed chlorine gas to exit the cylinder. The piston continues its upward motion, pushing the gas out of the cylinder and into the discharge line.
4. Intake and Exhaust: As the piston reaches the top of its stroke, the intake valve closes to prevent backflow of gas from the discharge line into the cylinder. Simultaneously, the exhaust valve opens to release any remaining gas from the cylinder, ensuring a complete discharge of the compressed chlorine gas.
5. Reciprocating Motion: The piston then reverses its direction and moves downward again, starting a new suction stroke and repeating the cycle. The reciprocating motion of the piston, driven by a motor or engine, continues to compress and discharge the chlorine gas.
6. Compression Ratio: The compression ratio is the ratio between the discharge pressure and the suction pressure of the chlorine gas. It determines the degree of compression achieved in each cycle. The compression ratio is an important parameter that affects the efficiency and performance of the compressor.
7. Cooling and Lubrication: Chlorine gas compressors require effective cooling and lubrication systems to maintain proper operating conditions. The compression process generates heat, and excessive heat can lead to equipment damage or safety hazards. Cooling mechanisms, such as water jackets or fins, are employed to dissipate heat from the cylinders and maintain the desired temperature range. Lubrication is vital to reduce friction between moving parts and ensure smooth operation, typically using compatible lubricants that are resistant to chlorine gas.
8. Safety Considerations: Chlorine gas is highly toxic and poses significant safety risks. Chlorine gas compressors are designed with safety features to mitigate these risks. These features can include gas leak detection systems, emergency shutdown mechanisms, ventilation systems to prevent the buildup of chlorine gas, and appropriate materials for handling chlorine gas, such as corrosion-resistant alloys.
9. Control and Monitoring: Chlorine gas compressors often incorporate control and monitoring systems to ensure safe and efficient operation. These systems can include pressure sensors, temperature sensors, vibration monitoring, and control panels that allow operators to monitor and adjust operating parameters, detect abnormal conditions, and respond appropriately.
10. Maintenance and Service: Regular maintenance is crucial to ensure the reliability and longevity of a chlorine gas compressor. Maintenance activities can include inspection of valves, cylinder walls, and piston rings for wear, cleaning or replacement of filters and scrubbers, lubrication of moving parts, and overall system checks. It is essential to follow the manufacturer's maintenance recommendations and guidelines to maximize the performance and safety of the compressor.
It's important to note that compressing chlorine requires careful attention to safety due to its hazardous nature. Chlorine compressors are designed with materials and components that are compatible with chlorine gas and are equipped with safety features like leak detection systems, proper ventilation, and emergency shutdown mechanisms.
Additionally, chlorine compressors often incorporate specialized materials and coatings to resist the corrosive properties of chlorine gas and prevent contamination. Regular maintenance and adherence to safety protocols are essential for the safe and efficient operation of chlorine gas compressors.
【男生把困困放到女生困困视频高清】注册登录

Hi! Welcome back.
How are you doing?
Let s talk! We’ll provide the perfect solution for you!
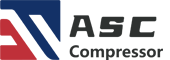
Since its establishment, ASC Compressor has focused on comprehensive solutions for Oilfield industry, CNG/LNG industry, Environmental protection, and Industrial compression. It has excellent quality in designing, researching, producing and manufacturing.
- Quick Link > Home > Products > Applications > News > About > Contact
-
Contact Us
- E-Mail: [email protected]
- Tel: +8618098536798/+86(0)5633698699
- Fax: +86(0)5633698699
-
Address:
No. 17 Xingye Road, Economic Development Zone, Xuanzhou District, Xuancheng City, Anhui Province, China