【lutu轻量版线路检测页】最新入口
-
Introduction to Components, Maintenance, and Working Principles of Rich Gas Compressors
Jun 05, 2024 -
Components and maintenance of hydrogen compressors
Apr 27, 2024 -
Characteristics of hydrogen compressors in different industries
Jun 24, 2024 -
Methods and steps for natural gas recovery
Jun 14, 2024 -
Some key points about off gas compressors
May 18, 2024 -
Coalbed Methane And Coalbed Methane Recovery Compressor
May 26, 2024
lutu轻量版线路检测页【乾坤易变】Jul 10, 2024
by:Anhui Shengnuo Compressor Manufacturing Co.,Ltd
Follow Us:
Natural gas compressors are essential equipment used in the natural gas industry to increase the pressure of the gas for transportation, storage, or processing purposes. They play a crucial role in maintaining the flow and efficiency of natural gas throughout the production and distribution process. Here are some technical parameters and key aspects related to natural gas compressors:
1. Compression Ratio:
- Compression ratio refers to the ratio of the discharge pressure of the gas to its suction pressure.
- The compression ratio determines the degree to which the gas is compressed and affects the power requirements and efficiency of the compressor.
- It is calculated as the absolute discharge pressure divided by the absolute suction pressure.
2. Flow Rate:
- Flow rate, also known as capacity or volumetric flow rate, represents the volume of gas that a compressor can handle per unit of time.
- It is usually expressed in standard cubic feet per minute (scfm) or cubic meters per hour (m³/h).
- The flow rate requirement depends on factors such as the demand for natural gas, pipeline capacity, and the specific application.
3. Discharge Pressure:
- Discharge pressure is the pressure at which the compressed gas is delivered by the compressor.
- The discharge pressure is determined based on the requirements of the downstream processes or the transportation system.
- It is typically measured in pounds per square inch (psi) or bar.
4. Horsepower (HP) or Kilowatt (kW) Rating:
- The horsepower or kilowatt rating indicates the power requirement of the compressor motor to drive the compression process.
- The power rating depends on factors such as the compression ratio, flow rate, and efficiency of the compressor.
- It is important to select a compressor with an appropriate power rating to ensure efficient operation and meet the desired gas compression needs.
5. Efficiency:
- Compressor efficiency is a measure of how effectively the compressor converts the input power into the desired compression output.
- The efficiency of a compressor is influenced by factors such as the type of compressor, compression ratio, operating conditions, and design features.
- Higher efficiency results in reduced energy consumption and operating costs.
6. Compressor Types:
- There are different types of natural gas compressors, including reciprocating compressors, centrifugal compressors, and screw compressors.
- Reciprocating compressors use pistons to compress the gas, while centrifugal compressors use rotating impellers.
- Screw compressors utilize two interlocking helical rotors to compress the gas.
- The selection of the compressor type depends on factors such as the required flow rate, pressure ratio, gas composition, and application-specific considerations.
7. Safety and Environmental Considerations:
- Safety features, such as pressure relief valves, temperature monitoring, and automatic shutdown systems, are incorporated into compressor designs to ensure safe operation.
- Environmental considerations include emissions control measures and compliance with regulations to minimize air pollution and greenhouse gas emissions.
Natural gas compressors are utilized in various industries for different applications. The performance requirements and characteristics of natural gas compressors can vary depending on the specific industry and application. Here are some examples:
1. Oil and Gas Industry:
- Upstream Exploration and Production: Natural gas compressors are used in upstream operations to boost the pressure of produced gas for transportation through pipelines or injection into reservoirs for enhanced oil recovery (EOR).
- Performance Requirements: High compression ratios, high flow rates, reliability, and adaptability to varying gas compositions and operating conditions.
- Characteristics: Often reciprocating compressors or centrifugal compressors, designed to handle sour gas (containing hydrogen sulfide) and other impurities.
- Midstream Processing and Transmission: Compressors are employed in natural gas processing plants and pipeline transmission systems for gas compression and transportation.
- Performance Requirements: Maintaining pipeline pressure, ensuring efficient gas flow, meeting pipeline capacity demands, and minimizing pressure drop.
- Characteristics: Centrifugal compressors or reciprocating compressors, designed for continuous operation, energy efficiency, and remote monitoring capabilities.
2. Power Generation:
- Natural gas-fired power plants utilize compressors to supply compressed gas for gas turbines or reciprocating engines.
- Performance Requirements: High pressure ratios, consistent flow rates, and reliability for power generation processes.
- Characteristics: Centrifugal compressors or reciprocating compressors, often integrated with power generation units, optimized for high efficiency, and low emissions.
3. Chemical and Petrochemical Industry:
- Compressors are used in various processes within the chemical and petrochemical industry, such as hydrogen production, ammonia synthesis, and ethylene production.
- Performance Requirements: Specific pressure and flow requirements based on the process demands, handling different gases and gas mixtures.
- Characteristics: Reciprocating compressors, centrifugal compressors, or screw compressors, tailored to the specific gas composition and process conditions.
4. Refining Industry:
- Compressors play a vital role in refinery processes like fluid catalytic cracking (FCC), hydrocracking, and hydrotreating.
- Performance Requirements: High compression ratios, handling various gases and gas mixtures, and ensuring reliable supply to downstream processes.
- Characteristics: Reciprocating compressors or centrifugal compressors, designed for high-pressure applications, resistance to corrosive gases, and compatibility with refinery processes.
5. LNG Industry:
- Natural gas compressors are used in liquefied natural gas (LNG) production and regasification facilities.
- Performance Requirements: Compressing natural gas for liquefaction or ensuring efficient regasification.
- Characteristics: Centrifugal compressors or reciprocating compressors, optimized for cryogenic conditions, capable of handling high flow rates, and maintaining reliability.
It's important to note that the performance requirements and characteristics mentioned above are general guidelines, and specific applications may have unique considerations. The selection and design of natural gas compressor in different industries depend on factors such as gas composition, pressure, flow rate, process requirements, energy efficiency, safety considerations, and compliance with industry standards and regulations. Working closely with compressor manufacturers and industry experts is crucial to ensure the appropriate selection and operation of compressors for specific industrial applications.
【lutu轻量版线路检测页】注册登录

Hi! Welcome back.
How are you doing?
Let s talk! We’ll provide the perfect solution for you!
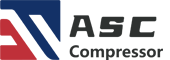
Since its establishment, ASC Compressor has focused on comprehensive solutions for Oilfield industry, CNG/LNG industry, Environmental protection, and Industrial compression. It has excellent quality in designing, researching, producing and manufacturing.
- Quick Link > Home > Products > Applications > News > About > Contact
-
Contact Us
- E-Mail: [email protected]
- Tel: +8618098536798/+86(0)5633698699
- Fax: +86(0)5633698699
-
Address:
No. 17 Xingye Road, Economic Development Zone, Xuanzhou District, Xuancheng City, Anhui Province, China