【com.缅甸AAAAA】最新入口
-
What mixed gases can a mixed gas compressor handle?
Jun 09, 2024 -
Types of mixed gas compressors and price examples
Apr 21, 2024 -
Some prominent butadiene compressor manufacturers in China
Jun 27, 2024 -
Common methods of recycling boil-off gas
Jun 22, 2024 -
piston gas compressor types, and price examples
May 13, 2024 -
How to choose a chlorine compressor
Jul 08, 2024
com.缅甸AAAAA【乾坤易变】May 20, 2024
by:Anhui Shengnuo Compressor Manufacturing Co.,Ltd
Follow Us:
A chlorine compressor is a specialized type of compressor designed specifically for handling chlorine gas. Chlorine compressors are used in various industries and applications where chlorine gas is required, such as water treatment, chemical manufacturing, and disinfection processes. Here are the main components that typically make up a chlorine compressor system:
1. Compressor Unit: The compressor unit is the core component of the system responsible for compressing the chlorine gas. It consists of a motor, a drive mechanism, and a compressor assembly. The compressor assembly can include components such as cylinders, pistons, valves, and seals that help in the compression process.
2. Piping and Connections: The chlorine compressor system includes a network of piping and connections that transport the chlorine gas to and from the compressor unit. These pipes are typically made of materials compatible with chlorine gas, such as stainless steel or other corrosion-resistant alloys.
3. Safety Devices: Chlorine compressor systems incorporate various safety devices to ensure safe operation and prevent potential hazards. These can include pressure relief valves, rupture discs, check valves, and emergency shutdown systems. Safety devices are crucial for protecting the system and personnel in case of overpressure or other abnormal conditions.
4. Gas Cooling System: Chlorine compression can generate heat, so a gas cooling system is often included to maintain the temperature within safe limits. This system may consist of heat exchangers, coolers, or water cooling systems that help dissipate the heat generated during compression.
5. Gas Dryers: Chlorine gas may contain moisture, which can be detrimental to the compressor and other downstream equipment. Gas dryers, such as desiccant dryers or molecular sieve units, are often incorporated into the system to remove moisture from the chlorine gas before it enters the compressor.
6. Control and Monitoring System: Chlorine compressor systems include control and monitoring systems to regulate and monitor various parameters, such as pressure, temperature, and flow rate. These systems may use sensors, gauges, and control panels to ensure proper operation and provide real-time information to operators.

7. Ventilation and Exhaust System: Chlorine compressors require proper ventilation and exhaust systems to handle any potential chlorine leaks or emissions. These systems help ensure a safe working environment by efficiently removing chlorine gas from the compressor room or facility.
8. Instrumentation and Instrumentation: Instrumentation and instrumentation devices, such as flow meters, pressure transmitters, temperature sensors, and level indicators, are used to measure and monitor various parameters within the chlorine compressor system. This information aids in maintaining optimal operation and detecting any abnormalities.
9. Material Compatibility: Chlorine gas is highly reactive and corrosive, so chlorine compressors are typically constructed using materials that are compatible with chlorine. Common materials used in the construction of chlorine compressors include stainless steel, nickel alloys, or other corrosion-resistant materials. These materials help ensure the longevity and integrity of the compressor system when handling chlorine gas.
10. Sealing Systems: Given the reactive nature of chlorine gas, sealing systems in chlorine compressors are designed to prevent leaks and maintain the integrity of the system. Specialized seals, such as chlorine-resistant elastomers or mechanical seals, are used to ensure tight sealing and minimize the potential for chlorine gas leakage.
11. Chlorine Gas Filtration: Chlorine gas may contain impurities or particulate matter that can affect the compressor's performance and longevity. Therefore, chlorine compressor systems often incorporate filtration units to remove contaminants from the chlorine gas before it enters the compressor. These filtration units can include activated carbon filters or other suitable filtration media.
12. Chlorine Gas Dosing: In certain applications, chlorine compressors may be used for dosing precise amounts of chlorine gas into a process or system. In such cases, the compressor system may include additional components, such as flow control valves, dosage measurement devices, or injection systems, to accurately control and monitor the dosage of chlorine gas.
13. Safety Considerations: Safety is of paramount importance when working with chlorine gas. Chlorine compressor systems should adhere to strict safety standards and regulations. This includes implementing safety features such as gas leak detection systems, emergency shutdown systems, and proper ventilation to ensure the safe handling of chlorine gas and protect personnel and equipment from potential hazards.
14. Maintenance and Service: Regular maintenance and service are essential for the reliable and efficient operation of chlorine compressor systems. This includes periodic inspections, lubrication, cleaning, and replacement of worn-out components. Following manufacturer-recommended maintenance schedules and guidelines helps ensure the longevity and optimal performance of the compressor system.
15. Compliance with Regulations: Chlorine compressor systems must comply with relevant industry regulations and standards to ensure safe operation and environmental protection. These regulations may include guidelines for chlorine gas handling, storage, and emissions control. Adhering to these regulations helps minimize risks and ensures responsible operation.
It's important to note that chlorine gas is hazardous, and working with chlorine compressor systems requires expertise and proper training. It is recommended to consult with professionals experienced in chlorine gas handling and follow industry best practices to ensure safe and efficient operation.
【com.缅甸AAAAA】注册登录
Maintenance of a chlorine compressor is crucial for ensuring its reliable and efficient operation while maintaining the safety of personnel and the environment. Here are some key aspects to consider when it comes to the maintenance of a chlorine compressor:
1. Regular Inspections: Conduct routine inspections of the compressor system to identify any visible signs of wear, corrosion, leaks, or damage. Inspect the compressor, piping, seals, valves, and other components for integrity and proper functioning. Pay attention to areas where chlorine gas may come into contact with the equipment, as corrosion can be a significant concern.
2. Lubrication: Follow the manufacturer's guidelines for lubrication to ensure proper lubrication of moving parts, such as pistons, cylinders, and bearings. Use lubricants recommended for chlorine service to prevent degradation or chemical reactions with the chlorine gas. Regularly check and replenish lubrication levels as necessary.
3. Seal Inspection and Replacement: Monitor the seals in the compressor system, such as piston rings or mechanical seals, to ensure they are functioning properly and effectively preventing leakage. Replace worn-out or damaged seals promptly to minimize the risk of chlorine gas leakage.
4. Filtration Maintenance: If the compressor system incorporates chlorine gas filtration units, follow the manufacturer's recommendations for maintenance and replacement of filtration media. Regularly clean or replace filters to ensure efficient removal of impurities and particulate matter from the chlorine gas.
5. Safety System Testing: Test and verify the functionality of safety devices and systems regularly. This includes pressure relief valves, rupture discs, gas leak detection systems, emergency shutdown systems, and ventilation systems. Ensure these safety features are operating correctly and promptly address any issues or malfunctions.
6. Control System Calibration: If the compressor system includes control and monitoring systems, periodically calibrate the sensors, gauges, and control panels to ensure accurate readings and proper operation. Maintain the control system software and firmware up to date, following the manufacturer's recommendations.
7. Preventive Maintenance Schedule: Develop a preventive maintenance schedule based on the manufacturer's guidelines and industry best practices. This schedule should outline routine maintenance tasks, including inspections, lubrication, seal replacement, and filter maintenance. Adhere to the schedule to prevent unexpected failures and optimize the compressor's performance.
8. Training and Documentation: Provide proper training to the maintenance personnel regarding the specific requirements of chlorine compressor maintenance. Ensure they are familiar with safety protocols, maintenance procedures, and potential hazards associated with chlorine gas. Maintain accurate records of maintenance activities, including inspections, repairs, and replacements.
9. Compliance with Regulations: Comply with applicable regulations and standards related to chlorine gas handling, storage, and emissions control. Stay updated with any changes in regulations and ensure the compressor system meets the required safety and environmental standards.
It is important to consult the manufacturer's documentation and guidelines specific to the chlorine compressor model being used, as they may provide detailed instructions on maintenance procedures, recommended spare parts, and other important considerations. Additionally, consider involving experts or professionals experienced in chlorine gas handling to ensure the safe and effective maintenance of the compressor system.
【com.缅甸AAAAA】平台地址

Hi! Welcome back.
How are you doing?
Let s talk! We’ll provide the perfect solution for you!
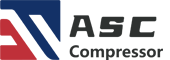
Since its establishment, ASC Compressor has focused on comprehensive solutions for Oilfield industry, CNG/LNG industry, Environmental protection, and Industrial compression. It has excellent quality in designing, researching, producing and manufacturing.
- Quick Link > Home > Products > Applications > News > About > Contact
-
Contact Us
- E-Mail: [email protected]
- Tel: +8618098536798/+86(0)5633698699
- Fax: +86(0)5633698699
-
Address:
No. 17 Xingye Road, Economic Development Zone, Xuanzhou District, Xuancheng City, Anhui Province, China