【不见星空全集完整免费观看高清版】最新入口
-
Types of mixed gas compressors and price examples
Apr 21, 2024 -
The relationship between Natural Gas Booster and Natural Gas Compressor
Jun 13, 2024 -
Compression of Ammonia and Application of Compressed Ammonia
Jul 23, 2024 -
The application industry and main functions of mixed gas compressors
Apr 19, 2024 -
Hydrogen Compressor Types And Working Principles
Apr 11, 2024 -
Price range of Natural Gas Compressors with different cooling methods
Jun 16, 2024
不见星空全集完整免费观看高清版【乾坤易变】Jun 05, 2024
by:Anhui Shengnuo Compressor Manufacturing Co.,Ltd
Follow Us:
A rich gas recovery compressor is a specific type of compressor designed for handling rich gas streams, which typically contain higher concentrations of heavier hydrocarbon components. These compressors are used to increase the pressure of the rich gas for further processing, transportation, or storage.
【不见星空全集完整免费观看高清版】注册登录
The working principles of a rich gas recovery compressor involve the compression of the rich gas stream to increase its pressure for further processing or transportation. Here's a general overview of the working principles:
1. Inlet and Suction: The rich gas stream enters the compressor through an inlet. The compressor is equipped with suction valves that open to allow the gas to enter the compression chamber.
2. Compression Chamber: Inside the compressor, the gas is trapped in the compression chamber. The chamber consists of a rotating impeller or a reciprocating piston, depending on the type of compressor. The impeller or piston is driven by an electric motor or a prime mover.
3. Compression Cycle: As the impeller or piston rotates or moves back and forth, it creates a pressure difference within the compression chamber. This pressure difference causes the gas to be drawn into the compression chamber and subsequently compressed.
4. Compression and Discharge: The impeller or piston compresses the gas by reducing the volume of the compression chamber. This compression increases the pressure of the gas. The compressed gas is then discharged from the compressor through a discharge valve.
5. Cooling and Lubrication: During the compression process, the gas temperature rises due to the increased pressure. To prevent overheating, compressors are often equipped with cooling systems, such as air or water cooling, to maintain the desired temperature range. Lubrication systems are also employed to reduce friction and ensure smooth operation of the compressor components.
6. Control and Monitoring: Compressors are typically equipped with control systems to regulate the compression process. These systems monitor parameters such as pressure, temperature, and flow rates to ensure optimal performance and safety.
7. Outlet: The compressed gas is discharged from the compressor at a higher pressure than the inlet pressure. It can then be directed to further processing units or transported through pipelines or other means to its intended destination.
Rich gas recovery compressors are designed to handle the specific characteristics of rich gas streams, which may contain higher concentrations of heavier hydrocarbon components. The compressor's design and materials are selected to handle the composition, pressure, and temperature requirements of the rich gas stream for efficient and reliable compression.
【不见星空全集完整免费观看高清版】平台地址
A rich gas recovery compressor consists of several key components that work together to facilitate the compression process. Here are the main components typically found in a rich gas recovery compressor:
1. Inlet and Suction System: This component includes the inlet connection and suction piping through which the rich gas stream enters the compressor. It usually incorporates suction valves that open and close to control the flow of gas into the compression chamber.
2. Compression Chamber: The compression chamber is where the actual compression of the gas takes place. It consists of a rotating impeller or a reciprocating piston, depending on the type of compressor. The impeller or piston is driven by an electric motor or a prime mover.
3. Discharge System: The discharge system is responsible for directing the compressed gas out of the compressor. It typically includes a discharge valve that opens and closes to regulate the flow of gas out of the compression chamber.
4. Cooling System: Rich gas compression generates heat, so compressors are equipped with cooling systems to prevent overheating. These systems can include air-cooling or water-cooling mechanisms that remove excess heat from the compressor's components and the compressed gas.
5. Lubrication System: Compressors require proper lubrication to reduce friction and ensure smooth operation. The lubrication system supplies lubricating oil to the moving parts, such as bearings, pistons, or impellers, to reduce wear and tear and improve overall efficiency.
6. Control and Monitoring System: Compressors are equipped with control systems that monitor and regulate various parameters during operation. These systems can include pressure sensors, temperature sensors, flow meters, and control valves. They ensure that the compressor operates within safe operating limits and can maintain the desired compression performance.
7. Drive System: The drive system provides the power needed to rotate the impeller or reciprocate the piston. It can consist of an electric motor, a gas turbine, a diesel engine, or other prime movers, depending on the specific application and power requirements.
8. Mounting and Frame: Compressors are typically mounted on a sturdy frame or base to provide stability and support. The frame also helps in reducing vibrations and noise generated during operation.
These components work together to facilitate the compression of the rich gas stream, increasing its pressure for further processing or transportation. The specific design and configuration of these components may vary depending on the type and size of the compressor, as well as the requirements of the rich gas recovery application.
【不见星空全集完整免费观看高清版】娱乐全站
Proper maintenance of a rich gas recovery compressor is essential to ensure its reliable and efficient operation. Regular maintenance helps prevent breakdowns, extends the equipment's lifespan, and minimizes downtime. Here are some key maintenance practices for a rich gas recovery compressor:
1. Inspection and Cleaning: Regularly inspect the compressor for any signs of wear, damage, or leaks. Clean the compressor and its components, including the inlet and discharge systems, cooling system, and lubrication system, to remove dirt, debris, and contaminants that can affect performance.
2. Lubrication: Follow the manufacturer's guidelines for lubrication, including the type of lubricating oil and the recommended intervals for oil changes. Ensure that the compressor's lubrication system is functioning properly and maintain the appropriate oil levels to reduce friction and protect the moving parts.
3. Filter Replacement: Replace air, oil, and gas filters as recommended by the manufacturer. Clean or replace clogged or dirty filters promptly to maintain proper airflow, prevent contamination, and ensure optimal performance.
4. Cooling System Maintenance: Inspect and clean the cooling system regularly to remove dirt, debris, and scale buildup that can impede heat transfer. Check coolant levels, monitor temperature and pressure gauges, and ensure that cooling fans or water circulation systems are functioning correctly.
5. Tightening and Alignment: Periodically check and tighten bolts, fasteners, and connections to ensure that the compressor remains securely mounted. Verify the alignment of the compressor shaft and bearings to prevent undue stress and wear on components.
6. Vibration Analysis: Monitor and analyze vibrations in the compressor using vibration sensors or monitoring systems. Excessive vibration can indicate misalignment, unbalanced rotating parts, or other issues. Address any vibration problems promptly to prevent further damage.
7. Performance Monitoring: Regularly monitor and record important performance parameters such as pressure, temperature, flow rates, and power consumption. Compare these values against established baselines to identify any deviations or changes that may indicate potential issues.
8. Scheduled Maintenance Tasks: Follow the manufacturer's recommended maintenance schedule for specific tasks such as belt replacement, valve inspection, piston ring replacement, and other routine maintenance procedures. Adhere to the schedule and carry out the necessary tasks to keep the compressor operating optimally.
9. Training and Documentation: Ensure that operators and maintenance personnel receive proper training on compressor maintenance procedures and safety protocols. Maintain comprehensive documentation of maintenance activities, including records of inspections, repairs, replacements, and any modifications made to the compressor.
10. Regular Performance Testing: Periodically conduct performance tests on the compressor to assess its efficiency and capacity. These tests help identify any degradation in performance and allow for adjustments or repairs as needed.
It's important to consult the compressor manufacturer's maintenance guidelines and recommendations specific to your equipment. Additionally, consider engaging qualified technicians or experts in compressor maintenance to carry out more complex tasks and ensure compliance with safety standards.
【不见星空全集完整免费观看高清版】体育直播

Hi! Welcome back.
How are you doing?
Let s talk! We’ll provide the perfect solution for you!
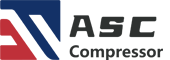
Since its establishment, ASC Compressor has focused on comprehensive solutions for Oilfield industry, CNG/LNG industry, Environmental protection, and Industrial compression. It has excellent quality in designing, researching, producing and manufacturing.
- Quick Link > Home > Products > Applications > News > About > Contact
-
Contact Us
- E-Mail: [email protected]
- Tel: +8618098536798/+86(0)5633698699
- Fax: +86(0)5633698699
-
Address:
No. 17 Xingye Road, Economic Development Zone, Xuanzhou District, Xuancheng City, Anhui Province, China