【两年半社区】最新入口
-
Methods and steps for natural gas recovery
Jun 14, 2024 -
Types and features of boil-off gas compressor
Jun 22, 2024 -
Main components and maintenance of a CNG standard station compressor
May 31, 2024 -
Types and features of Ammonia Compressors
Jul 24, 2024 -
The causes and prevention methods of natural gas compressor leakage
Jul 02, 2024 -
Hydrogen Compressor Types And Working Principles
Apr 11, 2024
两年半社区【乾坤易变】Jun 23, 2024
by:Anhui Shengnuo Compressor Manufacturing Co.,Ltd
Follow Us:
The working principles of a boil-off gas compressor are based on the fundamental principles of compression and gas dynamics. The compressor's main function is to increase the pressure of the boil-off gas, allowing for its further processing, utilization, or storage. Here is a general overview of the working principles of a boil-off gas compressor:
1. Gas Intake: The boil-off gas, which is generated due to heat ingress into the storage or transportation system, is drawn into the compressor through an inlet. The gas typically enters the compressor at a low pressure and temperature.
2. Compression Chamber: The compressor consists of a compression chamber, which is where the compression of the gas takes place. The chamber contains various components, such as rotors, impellers, or pistons, depending on the compressor type.
3. Compression Process: As the boil-off gas enters the compression chamber, it encounters the rotating or reciprocating components. These components create a pressure differential, causing the gas to be compressed. The compression process reduces the gas volume and increases its pressure.
4. Heat Dissipation: During the compression process, the temperature of the gas may increase due to the adiabatic compression effect. To prevent excessive temperature rise, some compressors employ cooling mechanisms, such as intercoolers or heat exchangers, to dissipate the heat generated during compression.
5. Discharge: Once the gas is compressed to the desired pressure level, it is discharged from the compressor through an outlet. The high-pressure gas can then be further processed, utilized, or stored, depending on the specific application.
6. Control Systems: Boil-off gas compressors often incorporate control systems to monitor and regulate the compression process. These systems may include sensors, valves, and control algorithms to adjust the compressor operation based on factors such as gas flow rate, pressure, and temperature.
It's important to note that the specific working principles of a boil-off gas compressor can vary depending on the compressor type (e.g., reciprocating, centrifugal, screw, etc.). Each type operates based on its unique design and mechanisms for gas compression. However, the underlying principle of increasing the gas pressure remains consistent across all compressor types.
The working principles described above provide a general understanding of how a boil-off gas compressor operates. The intricacies and specific details of the compression process may vary depending on the compressor's design, configuration, and manufacturer specifications.
【两年半社区】注册登录
A boil-off gas compressor consists of several key components that work together to facilitate the compression process and ensure the efficient operation of the compressor. While the specific components can vary depending on the compressor type and design, here are some common components found in a boil-off gas compressor:
1. Compression Chamber: The compression chamber is the main part of the compressor where the gas compression occurs. It houses the components responsible for compressing the gas, such as pistons, rotors, impellers, or scrolls.
2. Inlet and Outlet: The compressor has an inlet where the boil-off gas enters the compression chamber and an outlet through which the compressed gas is discharged. These ports are typically equipped with valves or other control elements to regulate the gas flow.
3. Drive System: The drive system provides the mechanical power to operate the compressor. It typically includes an electric motor, engine, or turbine that drives the rotating components of the compressor, such as pistons, rotors, or impellers.
4. Seals and Bearings: Seals are used to maintain the integrity of the compression chamber and prevent gas leakage. Bearings support the rotating components and ensure smooth operation. These components are crucial for minimizing energy losses and maintaining the compressor's efficiency.
5. Cooling System: Many boil-off gas compressors incorporate cooling systems to dissipate the heat generated during compression. This can include intercoolers, aftercoolers, or heat exchangers that help reduce the gas temperature and prevent overheating.
6. Lubrication System: Compressors often require lubrication to minimize friction and wear between moving components. Lubricating oil is circulated throughout the compressor to ensure smooth operation and extend the lifespan of the compressor.
7. Control and Monitoring Systems: Boil-off gas compressors are equipped with control and monitoring systems to regulate the compression process and ensure safe and efficient operation. These systems can include sensors, valves, pressure gauges, temperature sensors, and control algorithms to monitor and adjust key parameters during operation.
8. Safety Devices: Safety devices are essential for protecting the compressor and the overall system. These can include pressure relief valves, temperature sensors, and shutdown mechanisms that activate in the event of abnormal operating conditions or emergencies.
The specific configuration and arrangement of these components may vary depending on the compressor type and manufacturer. It's important to consult the compressor's documentation or the manufacturer's specifications for detailed information on the specific components and their functionalities in a particular boil-off gas compressor.
【两年半社区】平台地址
Proper maintenance of a boil-off gas compressor is crucial to ensure its reliable operation, optimize performance, and extend its lifespan. Regular maintenance helps identify and address potential issues before they escalate into major problems. Here are some key maintenance practices for a boil-off gas compressor:
1. Regular Inspections: Conduct routine visual inspections of the compressor to check for any signs of leaks, corrosion, vibration, or abnormal wear. Inspect the compressor components, including seals, bearings, valves, and connections, to ensure they are in good condition.
2. Lubrication: Follow the manufacturer's guidelines for lubrication, including the type and frequency of lubricant changes. Keep the lubrication system clean and well-maintained, and ensure proper lubrication of bearings, pistons, or other moving parts as per the manufacturer's recommendations.
3. Filter Maintenance: Clean or replace air and oil filters based on the recommended schedule. Clogged filters can reduce efficiency and may lead to increased wear and tear on the compressor components. Regularly inspect and clean or replace filters to maintain proper airflow and contamination control.
4. Cooling System Maintenance: If the compressor has a cooling system, inspect and clean heat exchangers, intercoolers, or aftercoolers to ensure efficient heat dissipation. Check coolant levels and quality, and follow the manufacturer's recommendations for maintenance and coolant replacement.
5. Control System Calibration: Periodically calibrate and test the control system, including sensors, pressure gauges, temperature sensors, and safety devices. Ensure that the control system is functioning accurately and that safety mechanisms are working correctly.
6. Vibration Analysis: Regularly monitor and analyze the vibration levels of the compressor using appropriate tools and techniques. Excessive vibration can indicate misalignment, imbalance, or other issues that may require corrective actions.
7. Regular Maintenance Tasks: Perform routine maintenance tasks such as tightening bolts and connections, inspecting electrical wiring and connections, checking for oil or gas leaks, and verifying proper operation of safety devices.
8. Scheduled Overhauls: Depending on the compressor type and manufacturer's recommendations, plan and execute scheduled overhauls to replace worn components, seals, gaskets, or other parts that have reached their service life. Follow the maintenance schedule provided by the manufacturer for these major maintenance activities.
9. Training and Documentation: Ensure that maintenance personnel are properly trained on the specific maintenance procedures and safety protocols for the boil-off gas compressor. Maintain accurate records of maintenance activities, including inspections, repairs, and component replacements.
It is important to consult the manufacturer's maintenance guidelines and recommendations specific to the boil-off gas compressor model being used. Following the manufacturer's instructions and considering the compressor's operating conditions will help ensure effective maintenance and optimal performance. Additionally, consider engaging qualified professionals or compressor service providers for complex maintenance tasks or major overhauls.
【两年半社区】娱乐全站

Hi! Welcome back.
How are you doing?
Let s talk! We’ll provide the perfect solution for you!
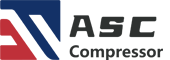
Since its establishment, ASC Compressor has focused on comprehensive solutions for Oilfield industry, CNG/LNG industry, Environmental protection, and Industrial compression. It has excellent quality in designing, researching, producing and manufacturing.
- Quick Link > Home > Products > Applications > News > About > Contact
-
Contact Us
- E-Mail: [email protected]
- Tel: +8618098536798/+86(0)5633698699
- Fax: +86(0)5633698699
-
Address:
No. 17 Xingye Road, Economic Development Zone, Xuanzhou District, Xuancheng City, Anhui Province, China